Let’s cut to the chase, shall we? Industrial engine maintenance is not just some fancy buzzword—it’s the backbone of keeping your operations humming like a well-oiled machine. Whether you’re running a small factory or a massive industrial complex, ignoring proper maintenance is like inviting disaster into your workplace. So, if you’re wondering how to keep your engines running strong without breaking the bank, you’ve come to the right place.
Now, I know what you’re thinking—“Maintenance sounds boring and complicated.” But trust me, it doesn’t have to be. In fact, with the right approach, industrial engine maintenance can save you time, money, and a whole lot of headaches. Think of it as giving your machinery a regular tune-up, just like you’d do for your car. The difference? Your industrial engines are probably worth way more than that old clunker in your garage.
So, buckle up because we’re diving deep into the world of industrial engine maintenance. We’ll cover everything from the basics to advanced techniques, so whether you’re a newbie or a seasoned pro, there’s something here for everyone. And hey, who knows? You might even learn a trick or two to impress your boss.
Read also:Find Your Sweet Treat The Ultimate Guide To Dubai Chocolate Bars
Why Industrial Engine Maintenance Matters
Alright, let’s get real here. Why should you care about industrial engine maintenance? Well, for starters, it’s all about keeping your business running smoothly. Downtime is the enemy of productivity, and when your engines break down, it’s like hitting a pause button on your entire operation. That’s not just inconvenient—it’s costly.
But it’s not just about avoiding downtime. Proper maintenance also extends the lifespan of your equipment. Think about it: would you rather replace an engine every few years or keep it running for a decade with some routine care? Exactly. Plus, maintaining your engines properly can improve efficiency, reduce energy consumption, and even lower your carbon footprint. Win-win-win, right?
And let’s not forget about safety. Neglecting maintenance can lead to serious accidents, putting your workers at risk. No one wants that. So, yeah, industrial engine maintenance isn’t just a good idea—it’s a necessity.
The Basics of Industrial Engine Maintenance
Before we dive into the nitty-gritty, let’s cover the basics. What exactly does industrial engine maintenance entail? At its core, it’s all about inspecting, cleaning, and repairing your engines to ensure they’re running at peak performance. But it’s not just about fixing things when they break. Preventive maintenance is key.
Here’s a quick rundown of the basics:
- Regular Inspections: Keep an eye on your engines and catch potential issues before they become big problems.
- Cleaning: Dust, dirt, and debris can wreak havoc on your machinery. Regular cleaning keeps things running smoothly.
- Lubrication: Oil and grease are your engine’s best friends. Make sure everything is properly lubricated to reduce wear and tear.
- Repairs: When something does break, fix it promptly to avoid further damage.
Simple, right? But don’t let the simplicity fool you. These basic steps are the foundation of a solid maintenance program.
Read also:Boys Over Flowers Cast Unveiling The Stars Behind The Iconic Drama
Common Challenges in Industrial Engine Maintenance
Of course, nothing in life is perfect, and industrial engine maintenance is no exception. There are plenty of challenges that can make even the most experienced technician pull their hair out. Let’s take a look at some of the most common ones:
1. Budget Constraints: Maintenance can be expensive, especially if you’re dealing with large, complex machinery. Finding the right balance between cost and effectiveness is crucial.
2. Lack of Skilled Labor: With the skills gap widening in many industries, finding qualified technicians can be tough. Investing in training and development is essential.
3. Time Management: Downtime for maintenance means lost productivity. Scheduling maintenance during off-peak hours or using predictive maintenance techniques can help minimize the impact.
4. Equipment Age: Older equipment may require more frequent maintenance and can be harder to repair. Upgrading to newer, more efficient models might be worth considering in the long run.
Advanced Techniques for Industrial Engine Maintenance
Now that we’ve covered the basics, let’s talk about some advanced techniques that can take your maintenance game to the next level. These aren’t just for the pros—they’re tools and strategies that anyone can use to improve their maintenance processes.
Predictive Maintenance
Predictive maintenance uses sensors and data analytics to predict when equipment is likely to fail. By monitoring things like vibration, temperature, and pressure, you can catch issues before they become critical. This approach can significantly reduce downtime and save you money in the long run.
Condition Monitoring
Condition monitoring is all about keeping a close eye on the health of your equipment. Using tools like infrared thermography and oil analysis, you can detect early signs of wear and tear. It’s like giving your engines a regular check-up to make sure everything’s in tip-top shape.
Remote Monitoring
In today’s connected world, remote monitoring is becoming increasingly popular. By using IoT devices and cloud-based systems, you can monitor your equipment from anywhere in the world. This is especially useful for companies with multiple locations or those operating in remote areas.
Data-Driven Maintenance Strategies
Data is the new oil, and when it comes to industrial engine maintenance, it’s your best friend. By collecting and analyzing data from your equipment, you can make informed decisions about when and how to perform maintenance. Here are a few ways data can help:
- Identify Trends: Analyzing data over time can reveal patterns and trends that might not be immediately obvious. This can help you anticipate potential issues and plan accordingly.
- Optimize Schedules: Data can help you determine the optimal maintenance schedule for your equipment, ensuring you’re not over- or under-maintaining.
- Improve Efficiency: By understanding how your equipment performs under different conditions, you can make adjustments to improve overall efficiency.
Data-driven maintenance isn’t just a buzzword—it’s a game-changer. Embrace it, and you’ll be ahead of the curve.
Cost-Effective Maintenance Tips
We get it—maintenance can be expensive. But there are plenty of ways to keep costs down without sacrificing quality. Here are a few tips:
- Focus on Preventive Maintenance: As we’ve already mentioned, preventive maintenance is key to avoiding costly repairs down the line.
- Use Quality Parts: Cheap parts might save you money in the short term, but they’ll cost you in the long run. Invest in quality components that will last longer.
- Train Your Team: A well-trained team can handle many maintenance tasks in-house, reducing the need for expensive outside contractors.
- Implement a Maintenance Management System: Using software to manage your maintenance processes can help you stay organized and efficient.
Remember, cutting corners on maintenance might save you money now, but it’ll cost you in the end. Be smart about where you allocate your resources.
Environmental Considerations in Industrial Engine Maintenance
In today’s world, sustainability is more important than ever. When it comes to industrial engine maintenance, there are plenty of ways to reduce your environmental impact. Here are a few ideas:
1. Use Eco-Friendly Lubricants: Traditional lubricants can be harmful to the environment. Switching to eco-friendly alternatives can help reduce your carbon footprint.
2. Recycle Used Parts: Instead of throwing away old parts, consider recycling them. Many components can be reused or repurposed, reducing waste.
3. Optimize Energy Usage: By keeping your engines running efficiently, you can reduce energy consumption and lower your emissions.
4. Implement Green Practices: From using renewable energy sources to reducing water usage, there are plenty of ways to make your maintenance processes more environmentally friendly.
Case Studies: Real-World Examples of Successful Industrial Engine Maintenance
Talking about maintenance is one thing, but seeing it in action is another. Let’s take a look at a few real-world examples of companies that have successfully implemented industrial engine maintenance strategies:
Case Study 1: XYZ Manufacturing
XYZ Manufacturing was struggling with frequent equipment breakdowns and high maintenance costs. By implementing a predictive maintenance program, they were able to reduce downtime by 40% and cut maintenance costs by 30%. Impressive, right?
Case Study 2: ABC Energy
ABC Energy faced challenges with aging equipment and a lack of skilled labor. By investing in remote monitoring and training programs, they were able to improve efficiency and extend the lifespan of their equipment. Their efforts paid off big time, with a 25% increase in productivity.
Future Trends in Industrial Engine Maintenance
The world of industrial engine maintenance is constantly evolving. Here are a few trends to watch out for:
1. Artificial Intelligence: AI is revolutionizing maintenance by providing insights and predictions that were once impossible to achieve.
2. Augmented Reality: AR is being used to train technicians and guide them through complex repairs, making the process faster and more efficient.
3. IoT Integration: As more devices become connected, the possibilities for remote monitoring and data collection are endless.
4. Sustainability: With growing concerns about climate change, companies are increasingly focusing on eco-friendly maintenance practices.
Conclusion: Take Action Today
And there you have it—your ultimate guide to industrial engine maintenance. From the basics to advanced techniques, we’ve covered everything you need to know to keep your machinery running smoothly. Remember, maintenance isn’t just a cost—it’s an investment in the future of your business.
So, what are you waiting for? Start implementing these strategies today. Whether it’s scheduling regular inspections, investing in predictive maintenance, or embracing new technologies, there’s no time like the present to take control of your maintenance program.
And don’t forget to share this article with your colleagues and friends. Knowledge is power, and the more people know about industrial engine maintenance, the better off we all are. So go ahead, spread the word, and let’s keep those engines running strong!
Table of Contents
- Why Industrial Engine Maintenance Matters
- The Basics of Industrial Engine Maintenance
- Common Challenges in Industrial Engine Maintenance
- Advanced Techniques for Industrial Engine Maintenance
- Predictive Maintenance
- Condition Monitoring
- Data-Driven Maintenance Strategies
- Cost-Effective Maintenance Tips
- Environmental Considerations in Industrial Engine Maintenance
- Case Studies: Real-World Examples of Successful Industrial Engine Maintenance
- Future Trends in Industrial Engine Maintenance
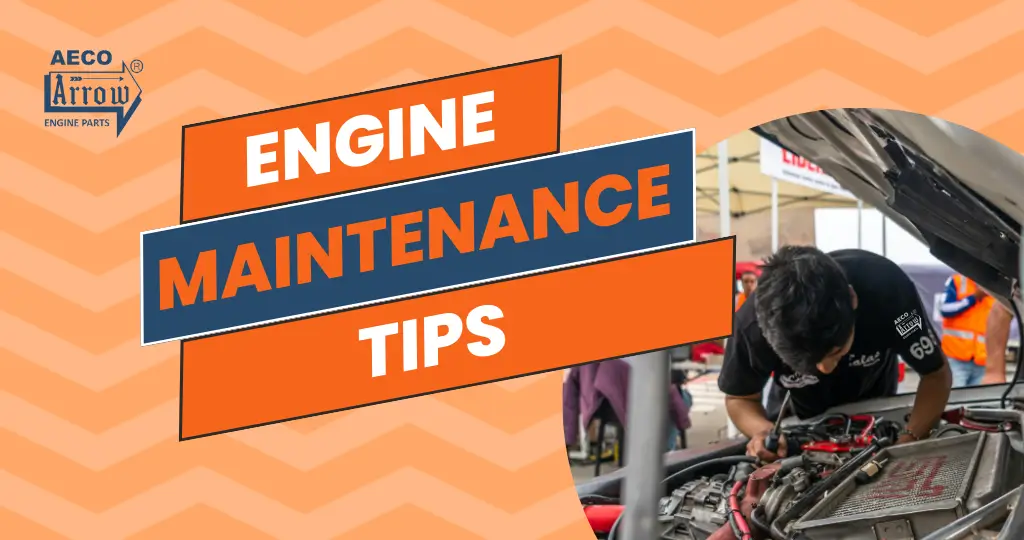
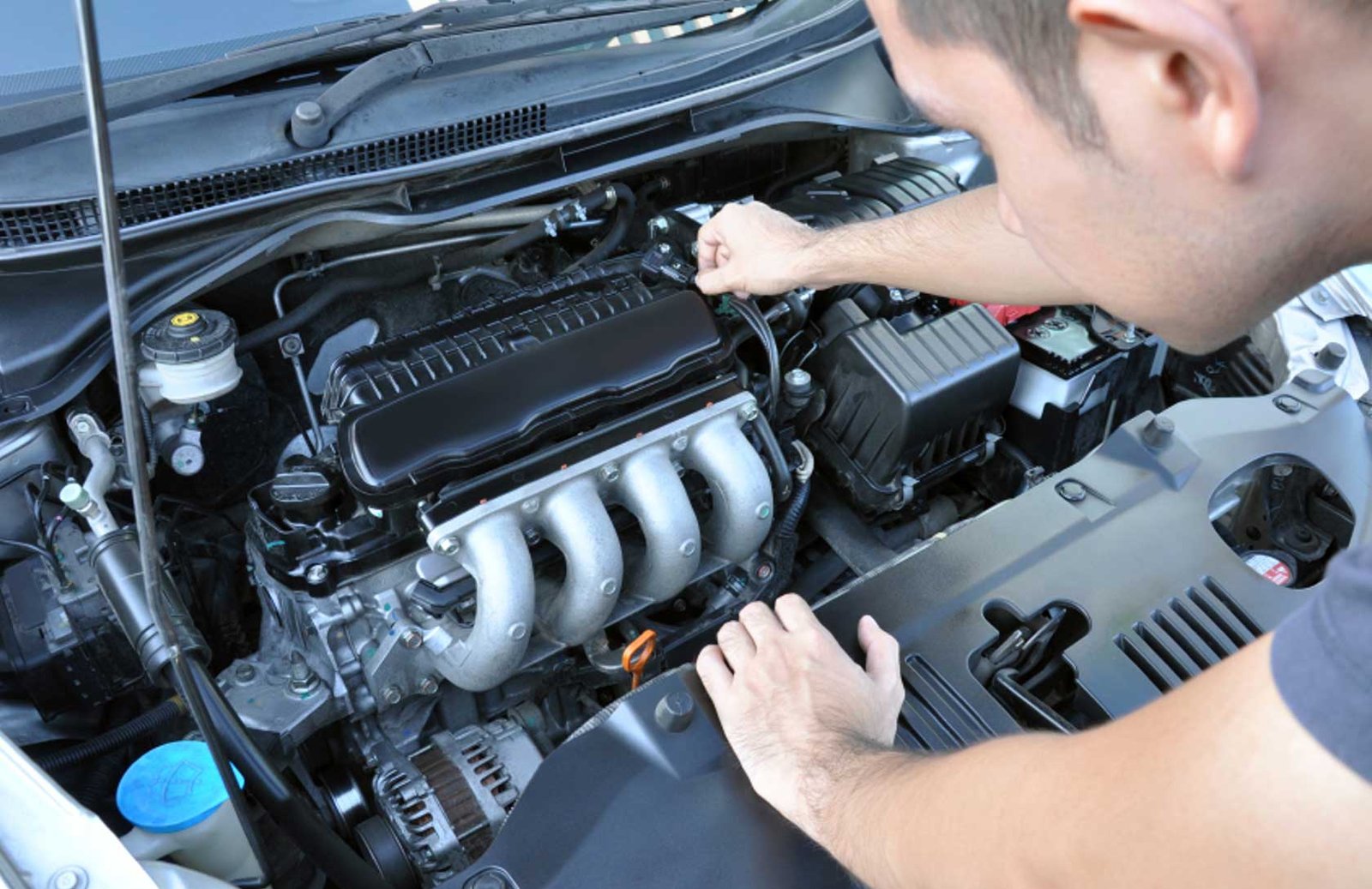
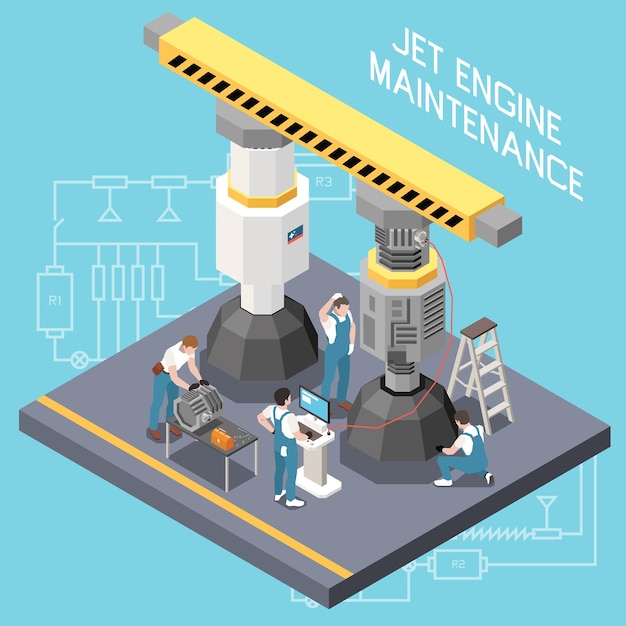